Cable trays are indispensable components in modern electrical installation projects, acting as cable management solutions that organize and support wiring systems. By simplifying the installation of electrical wiring and cable networks, they provide a reliable way to protect wires from mechanical damage and adverse environmental conditions. With many different types of cable trays available, it’s crucial to understand the various designs, materials, and installation methods to choose the most suitable tray for your project.
This guide will walk you through everything you need to know about cable trays: their purpose, types of designs, materials, manufacturing methods, fasteners, and how to match the right tray to your specific cable type.
The Purpose and Benefits of Cable Trays
The primary purpose of cable trays is to support and protect electrical wiring in various environments. They safeguard cables from mechanical damage, such as crushing or accidental cutting, and offer protection against harmful external conditions like moisture, dust, or corrosive agents.
Using cable trays also helps keep wiring organized, preventing cable tangling or overcrowding that could lead to overheating or malfunctions. They allow for the flexible routing of cables, making future expansions, repairs, or modifications much simpler. Additionally, by elevating cables off the ground and securing them in place, cable trays reduce potential hazards, contributing to a safer installation.
Other significant benefits of cable trays include:
– Easy Installation: Cable trays allow electricians to install large quantities of cables in a single run, reducing installation time and labor costs.
– Improved Safety: They reduce the risk of electrical shorts or fires by protecting the cables and maintaining proper spacing between them.
– Versatility: Cable trays can be customized for various applications, from industrial environments to residential buildings, and they can accommodate different cable types.
Key Types of Cable Tray Designs
Cable trays come in several distinct designs, each offering specific advantages based on the application, environment, and load-bearing needs. Understanding the characteristics of each type will help you choose the most appropriate one for your project.
1. Perforated Cable Trays
Perforated cable trays are one of the most widely used types in electrical installations. They feature small holes (perforations) that allow for natural ventilation, which helps prevent cables from overheating. These trays are typically used indoors, where there is no exposure to harsh weather conditions, and in locations where moisture or humidity is not a significant concern.
Advantages of perforated trays:
– Allows heat dissipation, preventing cables from overheating
– Suitable for indoor installations with minimal exposure to environmental elements
– Available in various sizes to accommodate different cable loads
Limitations:
– Not ideal for humid or wet environments, as moisture can seep through the perforations
2. Wire Mesh (Basket) Trays
Wire mesh trays, often referred to as basket trays, are made in the form of a grid or basket-like structure. These trays are particularly useful for lightweight wiring installations, such as telecommunications or data cables, where airflow and accessibility are important. The open design allows for excellent ventilation and easy inspection of the cables. However, wire trays do not provide protection from external elements like dust, moisture, or mechanical damage.
Advantages of wire mesh trays:
– Lightweight and easy to install
– Provides maximum ventilation, reducing the risk of overheating
– Ideal for IT, telecommunications, and control systems
Limitations:
– Offers minimal protection from environmental factors
– Not suitable for heavy or large-diameter cables
3. Solid Cable Trays
Solid cable trays are designed for environments where maximum protection is required. They do not have any perforations, providing a completely enclosed system that shields cables from dust, moisture, and mechanical damage. These trays are commonly used in industrial settings or outdoor environments where exposure to the elements is a concern.
Advantages of solid trays:
– Offers complete protection from environmental factors like moisture, dust, and debris
– Suitable for outdoor and industrial installations
– Ensures the integrity of the cable system in harsh conditions
Limitations:
– Lacks natural ventilation, which can lead to cable overheating in some applications
Cable Tray Manufacturing Methods
The method used to manufacture cable trays impacts their strength, durability, and load-bearing capacity. Depending on the installation environment and cable requirements, different manufacturing techniques are used.
1. Rolled Cable Trays
Rolled cable trays are produced from solid metal sheets, which are rolled into the desired shape. These trays are easy to manufacture and relatively inexpensive, making them popular for a variety of applications. Rolled trays can be either solid or perforated, depending on the need for ventilation.
Advantages:
– Affordable and widely available
– Suitable for both indoor and outdoor use (depending on the finishing)
– Perforated options allow for ventilation
Limitations:
– Can be heavy, especially in longer runs
2. Ladder Cable Trays
Ladder cable trays are constructed with side rails and rungs that resemble a ladder. The side rails provide strength, while the rungs offer support for the cables. These trays are designed to withstand heavy loads and are commonly used in industrial or large-scale power distribution systems. They also allow for natural ventilation and cable cooling.
Advantages:
– Can support heavy cables and withstand high loads
– Provides natural ventilation to prevent cable overheating
– Commonly used in power plants, mines, and outdoor installations
Limitations:
– Requires more installation time and labor due to its structure
3. Wire Trays
Wire trays, made from high-strength wire, are typically used for horizontal cable routes. They offer flexibility and are well-suited for lighter wiring systems such as telecommunications cables. However, because they are open, wire trays are not suitable for applications where environmental protection is critical.
Advantages:
– Lightweight and easy to install
– Allows for easy inspection and modification of cables
– Cost-effective for lightweight wiring applications
Limitations:
– Cannot withstand heavy loads or protect cables from external damage
Materials Used for Cable Trays
The choice of material for a cable tray is critical, as it directly affects its durability, weight, and resistance to environmental factors. The three most common materials used for cable trays are metal, plastic, and reinforced concrete.
1. Metal Cable Trays
Metal cable trays are the most common type used in electrical installations. They are typically made from steel, which is treated to resist corrosion. There are three main types of protective coatings applied to metal trays:
– Cold Galvanizing: A zinc coating is applied to protect against corrosion, but this method offers less durability than hot-dip galvanizing.
– Hot-Dip Galvanizing: This method involves dipping the steel into molten zinc, creating a thick, corrosion-resistant coating that makes the tray suitable for outdoor and industrial use.
– Enamel Coating: While enamel provides protection against minor damage, it is primarily used to improve the appearance of the tray and does not offer the same level of corrosion resistance as galvanizing.
Advantages of metal trays:
– Durable and strong, able to support heavy cables
– Can be used in a variety of environments, including industrial and outdoor installations
– Available in both perforated and solid designs
Limitations:
– Heavier than plastic or PVC trays
– More expensive than plastic trays
2. Plastic (PVC) Cable Trays
Plastic cable trays, particularly those made from PVC, are lightweight, flexible, and affordable. They are ideal for smaller installations where electrical conductivity and heavy loads are not a concern. PVC trays are also non-corrosive and are commonly used for routing telecommunications and data cables.
Advantages of plastic trays:
– Lightweight and easy to handle
– Non-corrosive and resistant to chemicals
– Flexible, making installation easier in tight spaces
Limitations:
– Less durable than metal trays
– Cannot support heavy loads
3. Reinforced Concrete Cable Trays
Reinforced concrete trays are specifically used for underground installations. They offer superior durability and protection from environmental factors, such as water and soil pressure. These trays are heavy-duty and ideal for applications where cables need to be protected from mechanical stress.
Advantages of reinforced concrete trays:
– Extremely durable and wear-resistant
– Provides excellent protection for underground cable routes
– Moisture-proof and resistant to mechanical damage
Limitations:
– Heavy and difficult to install
– Suitable only for underground installations
Types of Cable Tray Structures
Cable trays can be classified into several structural types, depending on the level of protection and ventilation required:
- Open Cable Trays: These trays allow for easy access to the cables and are used in applications where frequent maintenance or inspection is necessary. They provide minimal protection from environmental factors.
- Closed Cable Trays: Closed trays offer full protection for the cables from dust, moisture, and physical damage. They are typically used in environments where wiring needs to be shielded from external elements.
- Perforated Cable Trays: Perforated trays are partially open, allowing airflow to prevent overheating while offering some level of protection from dust and debris.
- Solid Cable Trays: These trays offer complete enclosure, ensuring that cables are fully protected from external factors like water, dust, and mechanical damage. However, they do not allow for airflow, so proper ventilation may be necessary in certain installations.
Fastening Methods for Cable Trays
The installation method for cable trays depends on their material and the environment in which they will be used:
- Reinforced Concrete Trays: These are typically installed in pre-prepared trenches for underground cable routing. Once the tray is placed in the trench, it is covered with soil to secure it in place.
- Metal and Plastic Trays: These trays are typically fastened to walls, ceilings, or other structures using brackets, clamps, or supports. The fastening method must ensure that the tray can bear the weight of the cables and withstand environmental stress.
Choosing a Cable Tray Based on Cable Type
Different types of cables require different types of cable trays to ensure proper protection and functionality:
– Sheet Metal Trays: Suitable for power cables and other general-purpose wiring. These trays are versatile and provide adequate protection in various environments.
– Wire Mesh Trays: Ideal for lightweight wiring systems, such as telecommunications or control cables. These trays offer excellent ventilation and are often used in ceiling installations.
– Ladder Trays: Designed for heavy-duty power cables and large-diameter wires. These trays can handle significant loads while providing natural ventilation to prevent overheating.
Conclusion
Choosing the right cable tray for your electrical installation project requires careful consideration of factors such as the tray’s design, material, and fastening method. By matching the cable tray to the specific needs of your wiring system, you can ensure the longevity, safety, and functionality of the installation. Whether you are working with power cables, telecommunications wiring, or underground installations, selecting the appropriate cable tray will make the installation process smoother and provide reliable protection for your cables.
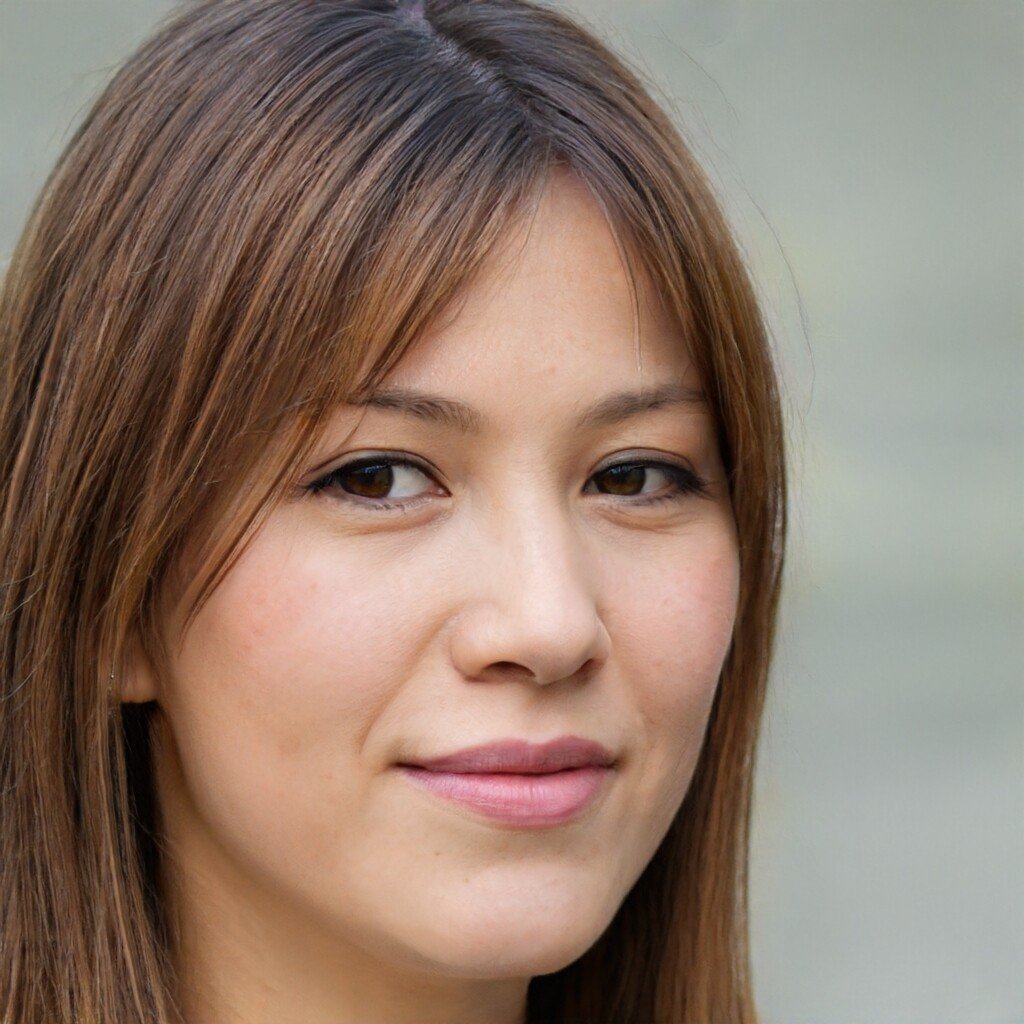
Baseball fan, risk-taker, band member, Vignelli fan and HTML & CSS lover. Doing at the nexus of aesthetics and purpose to create great work for living breathing human beings. My opinions belong to nobody but myself.